How to Finish a Basement Wall
Updated: May 12, 2023
Expert advice for a warm, dry and inviting basement

Multiple Days
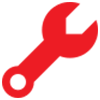
Intermediate
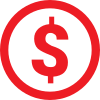
$101–250
Introduction
Finishing a basement is a perfect DIY project. For a fraction of the cost of an addition, you can convert basement space to valuable living space. Advances in waterproofing along with new products mean your basement rooms can be as dry and comfortable as any other room in the house.Tools Required
- Air compressor
- Air hose
- Caulk gun
- Chalk line
- Circular saw
- Corded drill
- Extension cord
- Framing square
- Hammer
- Hearing protection
- Knee pads
- Level
- Safety glasses
- Tape measure
- Utility knife
Materials Required
- 2x4 green treated lumber
- 2x4 lumber
- Rigid insulation
You can increase the living space in your house just by knowing how to finish and waterproof a basement wall. But there are a couple of important steps to take before you start.
Solve All Moisture Problems First
Before beginning any work, you must determine whether your basement has any moisture problems. If your foundation walls are only damp on humid summer days, fine—you’re good to go with the methods we recommend. But if you have any problems with standing or leaking water in the spring or during heavy rains, you’ve got some “prework” to do.
Fixes usually are as simple as adding or repairing gutters and downspouts or adjusting the grade to direct runoff water away from the house. But serious water problems may call for drastic measures like interior or exterior drain tiling, or exterior waterproofing, which could mean digging around the house or tearing up part of the slab.
You must solve all water problems, or you’ll risk boxing future water in behind a finished wall, ruining it. You’ll end up spending hundreds of bucks redoing a recently finished basement remodel. Find out the cost of finishing a basement.
Just about every carpenter or building inspector has a different opinion on how to finish a basement wall against masonry. The methods we’ll demonstrate work well in most conditions, but consult with your building inspector before beginning any work to make sure you’re meeting building codes in your area with these unfinished basement wall ideas.
Project step-by-step (14)
Seal the Wall
- Use a paint roller to apply the masonry waterproofing product you choose.
- Note: This step is only to help prevent water that naturally migrates through concrete through a capillary effect.
Install Blocking Between Joists
- Screw or nail one side of the block through the joist, and secure the other side to the sill plate.
- Pro tip: Use treated lumber if the brace will come in direct contact with bare concrete.
Install Foam Board Sheets
- Apply the adhesive vertically to keep water from pooling behind the foam insulation.
- Pro tip: Be sure you use XPS foam insulation—other types are not as moisture resistant.
Snap Lines on the Floor
- Snap a line on the floor 4 inches away from the foam as a guide for the bottom plate.
- Note: This will leave a 1/2-inch gap between the bottom of the new wall and the foam to allow a bit of wiggle room if the foundation walls aren’t perfectly plumb or straight.
Assemble the Walls on the Ground
- Sight every stud for a “crown” (a slight curve on the narrow side of the board), and mark an “X” on the crown.
- Have all the crowns face the same direction and assemble your wall with the crowns up.
- Note: That way, both ends of the studs are solidly on the ground when you attach the top and bottom plates, instead of acting like rockers on a rocking chair.
- Pro tip: Build the wall so it can be tipped right up. There’s usually not enough room to swing the whole wall around if you don’t.
Build the Walls Short
If you need to pound the walls into place with a sledgehammer, you’ve built your walls too tall. There’s no reason that the top plate has to be tight against the joists—that’s what shims are for. Measure the distance from the floor to the joists at several locations and build your wall at least 1/4 in. shorter than the shortest measurement. Trying to force a wall into place can raise the joists, which could wreak havoc with drywall joints and flooring on the rooms above.
Tip Up the Walls
- Tip a wall up with the bottom plate against the wall.
- Pro tip: If the floor joists are sagging or there’s ductwork in the way, you may have to lift the top of the wall in first and slide the bottom plate into place.
Fasten the Bottom Plate
- Put construction adhesive on the floor.
- Tip the wall into place and fasten with concrete nails or screws.
- Space fasteners every 6 feet and within 6 inches of each end.
Plumb the Wall and Secure the Top Plate
- Plumb the wall about every 4 feet.
- Pro tip: You need shims only about every third joist, but nail the top plate to every joist.
Build In Place When Necessary
If your floor is horribly out of level or if you’re framing around a window, it may be best to “stick frame,” nailing one stud at a time instead of building the wall on the floor.
Start by fastening your bottom plate, and then use a straight stud and a level to plumb up to find the location for your top plate. After you snap a line and fasten your top plate, plumb up again and mark the location of your first stud on both plates. Mark the rest of the stud locations on the plates using those marks. Toenail each stud into place with two nails on one side of the stud and one on the other.
Framing Inside Corners
- Turn the last stud on the first wall sideways and overlap it about halfway past the connecting wall to create drywall backing.