Cut down on the noise coming into or going out of your living area with these proven sound-dampening materials and techniques.

Multiple Days
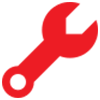
Beginner
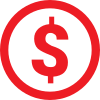
Varies
Introduction
Cut down on the noise coming into or going out of your living area with these proven sound-dampening materials and techniques.Tools Required
- Caulk gun
- Dust mask
- Screw gun
- Taping knife
- Tin snips
- Utility knife
Materials Required
- 1/2-in. plywood
- 5/8-in. drywall
- Acoustical dampening adhesive
- Cellulose insulation
- Door gasket
- Door sweep
- Drywall screws
- Electrical box extenders
- Fiberglass insulation
- Joint compound
- Resilient channel
- Silicone caulk
- Whisper clips
- Wood transition strip
- Work gloves
About Soundproofing Walls
In almost every way, the modern drywall-over-studs wall is better than its timber-and-masonry and plaster-and-lath ancestors. It’s fast and easy to build, lightweight and makes the most of inexpensive materials. But when it comes to stopping sound, the modern wall is a flop.
This article will show you how to make these walls (and ceilings) block sound better. Soundproofing walls involves ripping the existing drywall off the walls (and perhaps the ceiling), filling the walls with fiberglass insulation, attaching metal strips called “resilient channel” to the studs, and fastening new drywall to the channel.
This straightforward project to make your room soundproof doesn’t require specialized tools or high-level construction skills. Anyone who has experience hanging and taping drywall, along with a little carpentry and electrical know-how, can soundproof a room.
However, soundproofing is a messy, labor-intensive project. To minimize household havoc, it’s best to focus on one room at a time. The room might be a place that you want to keep sound out of—a home office, for example. Or it may be a room you want to keep sound in—like a home theater. Find out if it is possible to soundproof an entire house. Also, learn if putty pads help with soundproofing.
Editor’s Tip: There’s nothing more disruptive to a night of sleep than excessive sound apart from a cold chilly breeze, these seemingly minor noises can have an outsized impact on your well-being. So, turn to soundproof curtains to block out some of the din.
This project is also one of our home theater design ideas.
Project step-by-step (10)
Sound-Reducing Materials
Resilient channel acts as a spring between the drywall and studs. When sound waves strike a wall built with resilient channel, the drywall can vibrate independently without transferring the vibration to the studs. The metal channel is available at some home centers and all drywall suppliers.
- Fiberglass insulation batts are available at home centers. Although “acoustic batts” are available, plain old unfaced R-11 thermal insulation works just as well. Don’t spend more for R-13 batts; a higher R-value may actually cut the STC rating slightly.
- Type X 5/8-inch drywall is available at lumberyards and home centers. Type X drywall is meant for fire-resistance, but since it’s denser than standard drywall, it also stops sound better, especially when used with resilient channel.
- Acoustical sealant is available at drywall suppliers, but silicone caulk found at home centers is also a good choice for sound proof caulk. With either type, you’ll need lots of it and will probably save a few bucks by buying a big caulking gun that uses the more economical 30-ounce tubes.
- For attaching the channel to studs, use 1-1/4 inch screws. For attaching drywall to channel, use 1-inch screws. Fine-threaded screws grab on to resilient channel better than the coarse-threaded versions.
- Door gaskets, door sweeps and transition strips are available at home centers.
Move Electrical Boxes
- Turn off the power at the main panel before working on electrical systems.
- Move electrical boxes that share the same stud cavity so that they’re separated by at least one stud.
- To allow for the 1/2-inch resilient channel and 5/8-inch drywall you’ll use later, mount boxes so that the outer edge of the box is 1-1/8 inch from the stud.
- Pro tip: Boxes that don’t need to be moved can be repositioned so they protrude 1-1/8 in. Or you can use box extenders.
Seal the Boxes
- Use acoustical sealant or silicone caulk to seal around electrical boxes that serve adjacent rooms.
- Seal openings in the boxes, holes through studs and plates, and any openings in the drywall or framing.
Insulate the Walls
- Fill stud cavities with R-11 fiberglass batts.
- Note: The insulation should completely fill each cavity without open gaps or pockets.
- Split the insulation to fit around pipes or electrical cable.
- Cut the insulation with a utility knife so it fits squarely around electrical boxes.
- Pro tip: Wear gloves, a dust mask and eye protection when working with fiberglass.
Screw on Backer Strips
- Screw or nail strips of 1/2-inch plywood to wall framing around doors and along the floor.
- Note: The plywood simply provides a solid backing for nailing on door casing and baseboard later on. Resilient channel is springy and holds nails poorly.
- Stuff sound dampening insulation into the gaps around door jambs.
Attach the Resilient Channel
- Fasten the resilient channel to studs using 1-1/4 inch drywall screws.
- Note: The channels should be spaced no more than 24 inches apart on center, and the top of the upper channel must be below the top plate.
- Pro tip: Mount channels with the drywall flange up.
- Install channels so they don’t run more than 1 inch past studs.
- Overlap the ends.
- Pro tip: Resilient channel is easy to cut with aviation snips or metal shears.
Project Alternative: Soundproof a Wall Without Demolishing It
Cut holes at the top of each stud cavity and blow cellulose insulation into the cavities. Cut new 5/8-inch drywall so it’s 1/4 inch short of the floor and ceiling. Then attach the new drywall sheets using special acoustical dampening adhesive and drywall screws. Caulk the gaps with acoustical caulk.
Attach Drywall
- Mark the stud locations on the floor and ceiling so you can avoid them.
- Screw drywall to the channel’s flange with the drywall sheets running vertical. Use 1-1/4 inch fine-thread drywall screws spaced no more than 12 inches apart.
- Note: On ceilings, the sheets must run perpendicular to the channel.
- Pro tip: Screw into the channel, not into the studs.
Seal the Edges
- Fill the gap between the floor and drywall with acoustical sealant or silicone caulk.
- Seal cracks at the corners where walls meet other walls or the ceiling.
- Pro tip: Scrape away the excess sealant with a putty knife so you can finish these corners with joint compound as you normally would.
- Seal around electrical boxes.
Seal Doors with Gaskets
- Seal doors by applying adhesive-backed gaskets to the stop moldings.
- Note: This will make your door harder to close, and you may have to install an adjustable strike plate to compensate for the thickness of the gasket.
- Install “jamb extensions”—strips of wood that make the door jamb flush with the drywall.
Add a Transition Strip
- Seal the gap under a door with a door sweep and a wood transition strip.
- Note: A wood transition strip covers the joint where two types of flooring meet and provides a ridge for the sweep to seal against. Metal strips don’t work with sweeps because they aren’t thick enough.
Add a Door Sweep
- Screw a sweep to the back of the door, low enough so that it seals against the transition strip.
- Pro tip: If you have no need for a transition strip, you can use an automatic door sweep, which rises above the floor when the door opens and drops down when the door is closed.
Problem Areas
Ducts
The metal ducts of a forced-air heating/ cooling system are a noise fighter’s archenemy. They not only punch large holes in a room but also carry sound throughout a house. If there are metal ducts connected to the room you want quieted, listen to the sounds entering the room. If they’re primarily coming through the ducts, this insulation/resilient channel project won’t help, no matter how soundproof you make the walls. And unfortunately, there’s not much you can do about metal ducts, short of lining them with fiberglass or replacing them with fiberglass ducts (large, often impractical projects).
Floors
The best way to keep sound from passing through a floor or ceiling into the room above or below is to use insulation and resilient channel. Ripping drywall off a ceiling in a room where you’re stripping the walls anyway isn’t such a big deal. But if you want to keep sound from traveling through the floor of a room, you have to tear out the ceiling in the room below or buy an acoustical floor covering. The good thing about stripping a ceiling is that you can block off spaces between joists.
Note: If the sound coming through your ceiling is primarily “impact noise” (such as footsteps or toys slamming against the floor), the best fix is a heavy carpet and pad.
If your room is just above the basement, learn how to soundproof your basement ceiling to cut down on the noise.
Doors
A typical wood-panel or hollow-core door has an STC rating of about 17. By sealing between the jamb and wall framing, and adding weatherstripping gaskets and a door sweep (Photos 9 through 11), you can raise the STC to 20; that’s an easy, noticeable improvement, but maybe not enough.
A sound barrier is only as good as its weakest point. So if you go to the trouble of building a 50-STC wall with a 20-STC door, most of the benefit will be lost through the door. Keep this in mind when you decide whether or not to add insulation and sound channel to a wall with a door.
To reach an STC rating higher than 20, you have to replace your door and jamb. A well-sealed solid-core wood door has an STC of about 28. “Acoustical” wood doors with STCs in the 30-to-50 range are also available. Most lumberyards stock or can order interior solid-core doors, but for acoustical doors, your best bet is a supplier that caters to commercial construction.
Soundproofing Do’s and Don’ts
Here are some rules of thumb for stopping sound:
- Caulk like crazy. Your goal is an airtight room. Caulk around electrical boxes, light fixtures, and plumbing and heating lines. Seal up even the smallest holes and cracks. Remember, if air can pass through, so can sound.
- If you have old plaster-and-lath walls, don’t remove them to add insulation and resilient channel. Plaster-and- lath walls are good sound-stoppers. To improve them, just seal cracks and gaps.
- Removing ceiling drywall gives you a great opportunity to add light fixtures. If you choose recessed lights, buy those rated “IC” so you can surround them with insulation. Other recessed fixtures must not come in contact with insulation.
- You must remove existing drywall before installing resilient channel. Don’t simply attach the channel over existing drywall.
- If you go to the trouble of tearing off drywall, don’t cheat yourself by using resilient channel or insulation alone. Use them together and you’ll gain up to 15 STC points. But use either one alone and you’ll gain only four or five.
- Don’t bother attaching resilient channel to both sides of a wall. One side does the job.
- Don’t use resilient channel on steel studs. Steel studs absorb vibration by themselves, so there’s no need to use sound channel. A steel-stud wall with insulation alone performs about the same as a wood-framed wall with insulation and resilient channel. Don’t forget to check our tips to soundproof your basement ceiling.