Forge something new from something old.

A full day
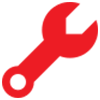
Professional
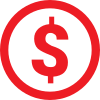
Varies
Introduction
An art form that spans millennia, bladesmithing recently has seen a surge in popularity. DIYers need to be careful, though — you just might find yourself with a new hobby or profession.
For Jason Kraus, that’s exactly what happened. For more than a decade he’s made swords, daggers and axes. Here, he’ll show us how to make a beautiful knife from an ugly railroad spike.Meet the Expert
A full-time bladesmith for more than 10 years, Jason Kraus has appeared on the hit shows Forged in Fire and Master of Arms. He operates Northstar Forge in Carver, Minnesota.
You’ll Need a Gas Forge
A gas forge is by far the most reliable and controllable type of forge to operate. Coal forges may have old-world charm, but they come with a steep learning curve. To get up to speed quickly, start with gas.
This forge is simple — a propane tank feeds a burner in an insulated chamber. Find one online for as low as $150; search for “gas forge for knife making.”
Tools Required
- Anvil
- Belt Sharpener
- Bench Grinder
- Forging Hammer
- Gas forge
- Safety Gear
- Tongs
Materials Required
- Railroad Spike
Project step-by-step (11)
Bring Up the Heat
After the forge has come up to temperature, get the steel up to working temperature. Jason secured the railroad spike in a set of tongs and placed it in the forge until it glowed bright orange — about 1,500 degrees.
Form the Handle
One of Jason’s favorite handle shapes is the simple twist. Once the railroad spike glowed orange, he put it in a vise and twisted it 360 degrees.
Draw Out the Blade
Once the handle was defined, Jason drew out material on the anvil. He didn’t aimed for a specific shape, just a uniform thickness of 1/4-inches.
Hammer the Blade Profile
After drawing out the blade material, Jason defined the curved profile of the blade edge by forging the shape with a hammer on the anvil.
Refine the Blade Shape
Using the grinding wheel, Jason refined the shape by putting a curve in the top of the blade. It’s easier to do this before the heat-treating process.
Normalize the Steel
Subjecting the steel to multiple heat cycles “normalizes” the particles of the steel, providing a uniform grain structure. Jason heated the blade in the forge and let it air cool five times.
- These two cross-sections of steel show the results of the normalization process. The steel on the left is perfectly normalized; the steel on the right, from a broken knife blade, is poorly normalized.
Quench the Blade
Once the blade was normalized, Jason set the knife back in the forge. He brought the temp up to 1,600 degrees — he could tell by the steel’s bright orange color — and quickly submerged the blade in quenching oil. This thoroughly hardened the steel.
Temper the Steel
The final step in the heat treatment process, “tempering” softens the steel ever so slightly to produce a blade edge that’s hard but not brittle. For railroad spike knives, Jason used a torch to bring the temperature to 375 degrees and let the blade air cool.
Grind a Final Time
After the steel was tempered, Jason ground down the blade profile to a fine edge with his belt grinder. To protect his fingers, he held the blade against the platen with a push stick. The blade looked sharp but wasn’t quite there.
Sharpen the Knife
Jason developed a strong, razor-sharp edge by holding the knife to the belt between the wheels, a process called slack-belt sharpening. With light, even pressure, he drew the blade across a progression of belts. Each was finer than the last, starting at 320 grit and stopping at 3,000 grit.
Jason’s tools
Bladesmithing calls for safety goggles, a leather apron and these heavy-duty tools.
Tongs
- Much like clamps in a wood shop, a forge cannot have too many tongs.
Anvil
- This 100-year-old anvil came from Sweden.
- A bladesmith uses an anvil and a hammer to draw out the steel and form the curves of the blade.
Wire brush
- Jason removes scale with a wire brush while he works the steel.
Rounding hammer
- Jason forged this 3-lb. hammer himself, and it’s one of his favorites. One side is rounded and the other flat.
- The rounded head draws out the steel.
- The flat side removes hammer marks and flattens the steel.
Torch
- Jason used a MAPP gas torch to temper our railroad spike knife. For everything else, he goes with an industrial oven.
The Twist-o-Matic 3000
- Jason made this tool himself by welding an adjustable wrench to a monkey wrench.
- He uses it to twist the railroad spike while it’s held in a vise.