How To Repair Long Sections of Leaking Copper Pipe
Updated: Jul. 16, 2024
5 simple steps to repair a leak.

A full day
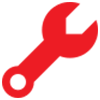
Intermediate
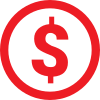
Less than $20
Introduction
You can fix leaky copper pipe quickly and efficiently with special repair sleeves. We show you how to cut and solder copper supply lines.Tools Required
- Tube cutter
Materials Required
- Emery cloth
- Flux and brush
- Solder
- Sweat coupling
Project step-by-step (4)
When a copper pipe corrodes and leaks or bursts from freezing, you have to fix it fast. If the leak is pinhole-sized and less than 1/2 in. of pipe must be removed, you can make the repair by cutting the pipe and soldering (“sweating”) on an ordinary pipe coupling.
However, to repair longer sections, you’ll want to use a “sweat” coupling, which you can find at home centers and well-stocked hardware stores. You can buy a sweat coupling sized to repair 1/2-in. or 3/4-in. copper pipe.
Cut the repair sleeve from the 12-in. repair coupling stock. Smooth the rough-cut inside edges of the sleeve by inserting the blade of the pipe cutter into the cut ends and turning the cutter until the sleeve slides over the pipe ends without snagging. Clean the sleeve’s inside edges for soldering with a 3/4-in. diameter wire fitting brush.
Cut out the damaged pipe
- First, shut off the main water supply valve and drain the damaged water line.
- If the leak isn’t obvious, it’s worth your time to mark it. That way you won’t miss part of it as you replace the damaged section.
- Using a pipe cutter, cut out a section of pipe that extends about 1 in. to each side of the leak.
- Start by gripping the pipe firmly in the cutter’s jaws and tightening the cutter’s screw.
- Rotate the cutter in the direction shown—as you tighten the screw handle—until the pipe snaps.
- After making the cut, measure the gap and, from the sweat coupling, cut a repair piece that’s 1 in. longer than the damaged section.
- The key to a good joint when soldering copper pipe is to keep the inside of the pipes dry, so keep a cotton rag stuffed in each pipe end to absorb dribbles of water until just before you solder.
- Tip: Open a faucet above that level to keep pressure from building up and dribbling more water into your repair.
Clean and flux mating surfaces
- Clean corrosion from the inside of the repair sleeve using a wire fitting brush.
- Clean the outside of the pipe with plumber’s sandcloth or emery paper.
- Brush flux onto all four cleaned surfaces.
Slide on the repair sleeve
- Slide an end of the sleeve first over one pipe and then slip it back over onto the other. You may have to loosen nearby pipe hangers.
- Center the sleeve over the pipe ends so that about 1/2 in. of each pipe is inside the sleeve.
Solder the joint
- Hold the tip of the torch flame to one side of the joint and hold the tip of the solder wire to the opposite side.
- Pull the solder away when enough of it melts to completely fill the joint.
- Once you’re finished, turn the main supply valve on and check for leaks.