Interior Trim Work Basics
Updated: Feb. 29, 2024
All the trim basics from start to finish, plus a clever way to get those miters tight

Multiple Days
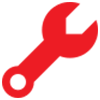
Intermediate
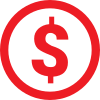
$101–250
Introduction
We show you how to make crisp, sharp corners and tight joints when installing door trim, window trim and a three-piece baseboard. With a few basic carpentry tools and a little patience, you can trim out a room in a weekend. And with a little practice you can master the two key trim techniques, mitering and coping.Tools Required
- 4-in-1 screwdriver
- Combination square
- Coping saw
- Drill bit set
- Drill/driver - cordless
- File
- Glue
- Hammer
- Miter saw
- Nail set
- Putty knife
Materials Required
- 3d finish nails
- 4d finish nails
- 6d finish nails
- 8d finish nails
- Wood putty
- Wood trim
In this article, we’ll show you the basic steps for installing a wide trim around a door and window, complete with mitered corners. We’ll also show you how to put in a built-up baseboard made from a combination of three types of moldings.
You’ll need several key tools to do a first-class interior trim molding job. Use a power miter saw for clean angle cuts. A power miter saw vastly simplifies the job because it allows you to make incredibly accurate cuts in a matter of seconds. Even professionals admit they couldn’t do the same quality of work without one. If you don’t have a power miter saw, you can rent one. If you’re renting a miter saw, cut several scrap pieces to get the feel of the tool before cutting your trim.
You’ll also need a coping saw. This saw has a narrow blade and tiny teeth that allow you to cut tight curves; it’s available at any hardware store. And here’s a tip: Avoid that annoying trip to the hardware store in the middle of your project—pick up a couple of spare blades in case you break one.
The photo below illustrates the trim carpenter lingo we’ll use in this how-to article.
Project step-by-step (25)
Get Set Up and Ready to Start
- Clear the room you want to trim out.
- Make your cuts in the middle of the floor.
- Put a fan in the window if dust is a problem.
Prefinishing Interior Trim Molding Saves a Ton of Time
Once you get your trim home, sand and stain or paint the trim before you install it. It’s a lot easier to finish trim before installation, working on sawhorses, than afterward, lying on the floor with sandpaper and a staining rag. Plus you can do a better job of sanding and finishing the pieces. After you’ve installed the pieces, be prepared to touch them up a bit. Do all the finish work in a well-ventilated area. Learn how to mill and install your own wood trim.
Project 1: Interior Door Molding Case
Mark the Reveal
- With a combination square, mark a reveal line 3/16 inch from the edge of the jamb.
- Pro tip: Use a sharp pencil and position the marks in the corners and about every foot along the jamb edge.
Cut Test Pieces
- Cut two 12-inch-long test pieces of the casing at opposite 45-degree angles on the power miter box.
- Use the test pieces to check the fit of your casing on the door jamb.
Check the Miter
- Hold the test pieces on the reveal marks to check the fit of the miter in the corner.
- Note: Even though the corners should be a perfect 90 degrees, often they’re not. In addition, if the jamb sticks out or is set back slightly from the wall, a 45-degree miter cut won’t fit tight. By holding the test pieces at the corner you can see exactly how your casings will fit.
- If the joint is even slightly open at the top or bottom of the miter, adjust the angle on the miter saw slightly, recut both pieces and check the fit again.
- Pro tip: Take your time — you may be surprised how tight you can get the joint to fit.
Cut the Side Casing
- Cut the side casing about 1/2 inch overlong and hold it in place on the door jamb along your reveal marks.
- Use a sharp pencil to transfer the top reveal mark from the head jamb to the side casing.
- Cut the miter at the angle you established with your test pieces.
Predrill and Tack
- Hold the side casing in place.
- Predrill nail holes every 12 to 16 inches, using a drill bit about 1/32 inch smaller than the nail size.
- Pro tip: Stay 1 inch away from the ends to avoid splitting.
- Drive 4d finishing nails into the jamb and 6d finishing nails into the wall.
- Note: If you’re using thicker casing, increase your nail size one increment, using 6d nails in the jamb and 8d nails in the wall. Your nails should penetrate the studs and the jamb at least 3/4 inches.
- Tack the casing into the jamb first, then to the wall.
- Pro tip: Wait until you’ve fit all the casings before you drive the nails in completely, in case something doesn’t fit right and you have to remove the trim to recut it.
Miter and Mark the Top Casing
- Cut the corresponding angle on the top casing, leaving the opposite side at least 1 inch overlong.
- Check your miter at the second corner with your test pieces, and adjust if necessary to fit tight.
- Mark the opposite corner on the top casing, cut it and tack it up.
Mark the Second Side Casing
- Cut the second side casing about 1 inch overlong.
- Hold the casing backward and parallel to the door jamb.
- Make a mark where the edge of the side casing intersects the upper edge of the top casing.
- Cut the side casing about 1/32 inch overlong.
- Slide the casing into place.
- Check your fit, and then trim it to its final length.
- Once the miter fits, nail the casing in place.
- Pro tip: You may have to slip a small shim behind one of the casings to align them.
Predrill the Corners
- Align the miters and predrill a 1/16-inch hole for 3d finish nails, one from the top and one from the side.
- Pro tip: Hold a piece of cardboard against the wall to prevent marring the wall while drilling.
Nail the Corners
- Drive the nails into the casing gradually, alternating between the two nails so the miter doesn’t slide out of alignment.
- Pro tip: Use cardboard again between the wall and the hammer to avoid marring the wall.
Set the Nails
- Tap the nails just below the surface with a hammer and a nail set.
Project 2: Case a Window
Begin With the Top Casing
- Trim a window using the same techniques as we showed for a door. However, cut and tack the top casing first. Then fit the sides and finish with the bottom.
Miter the Bottom Last
- Fit one miter on the bottom, then overlap the opposite miter and mark it.
- Cut the miter 1/8 inch overlong, slide the casing into place and trim it down gradually while checking the fit.
Project 3: Install Baseboard
Cut All the Base Extra Long
- Use a stud finder to locate the studs, and mark their location on the wall with a narrow piece of painter’s tape.
- Rough-cut all the baseboards about 2 inches overlong and lay them in place around the perimeter of the floor.
- Starting with the longest wall, cut the first piece to length and nail it into the studs with 6d finishing nails.
- Pro tip: Remember to predrill your holes. You can also put a small amount of glue at the miters and cross-nail them with 4d finishing nails.
- Continue around the room, cutting the inside corners off at 90 degrees and butting them together.
Cutting a Scarf Joint
If you have to splice two pieces on a wall, use a “scarf joint.” Cut a 30-degree angle on each piece; if the joint opens slightly, this angle will hide the crack. Select pieces with similar grain color and pattern so the joint is less visible. Always locate a splice over a wall stud.
Test Fit the Miters
- Miter two 1-foot test pieces and press them tightly against the outside corners to determine the correct angle.
- Adjust the miter saw to get a tight fit.
Cut the Miter to Length
- Hold the baseboard in place and mark the backside at the corner.
- Cut the piece to length at the predetermined angle for an exact fit.
Cut and Nail the Second Piece
- Cut the second piece to length at the same angle.
- Predrill, glue and nail the outside corner.
Corner Fitting Trick
If the drywall tapers in at the bottom of the wall or stops short of the floor, simply drive a screw at the bottom of the wall and turn it in until the head of the screw is at the same plane as the main wall. The head will prevent the baseboard from tipping in.
Cope Inside Corners of the Base Cap
- Run the base cap in the same order as the baseboard.
- To cope the inside corner of the base cap for a tight fit, first cut one end at a 45-degree angle as if you were cutting an inside miter.
Cut the Profile with a Coping Saw
- Use a coping saw to cut along the profile left by the miter.
- Pro tip: Angle your coping saw back slightly (back cut) to get a tighter fit on the face of the profile.
Test Fit the Cope
- Check the fit against the adjoining base cap in the corner.
Fine-Tune With a File
- Trim with a file as necessary.
- After fitting the cope, measure the cap for length, cut the other end and nail it up.
Add the Base Shoe
- Install the base shoe the same as the base cap, coping inside corners and mitering outside corners.
- Where the shoe meets the door casing trim, cut at a 30-degree angle the portion that sticks out.
- Predrill and nail the base shoe to the baseboard with 4d finishing nails.
Finish with Filler
- Set the nails and fill the holes with colored putty to match the wood stain.
- If necessary, mix two shades of putty together to get a good color match.
- Pro tip: With light-colored wood, always mix the color on the light side; darker putty stands out.
- Press the putty into the holes with your finger and wipe the excess off with a cloth.
Video: How to Trim a Door
Travis Larson, senior editor at The Family Handyman, will show you how to trim a door in about 10 minutes per side. The first time you do it, it will take longer but once you get the hang of it, you’ll be trimming out doors like a pro.
How to Shop for Interior Trim
Stock interior trim is available in a wide range of styles from most lumberyards and home centers. We chose a relatively wide (3-1/4 inches) beaded wood casing trim to go around our doors and windows. It’s 11/16 inches thick. We used three components to create the base: a 1/2-inch x 3-1/4 inch. “hook strip,” a 9/16-inch x 1-3/8 inch base cap, and a 7/16-inch x 3/4-inch base shoe (see “Interior Trim Terms,” above). Combine other standard trim types to create wider and more detailed shapes.
If you don’t find an interior trim molding style you like or you’re trying to match a molding in an older house, search“millwork” online. Millwork shops can custom-produce almost any type of interior trim from most species of wood. Custom work, however, comes at a price; be prepared to pay as much as three times the cost of stock moldings, plus setup charges. In addition, you may have to wait four to eight weeks.
Most interior door molding is made of solid wood or medium-density fiberboard with a wood veneer. Oak, pine, birch, maple and poplar are the most common types available. We chose maple for our project.
Sometimes you can find trim made of various types of plastic, most often prefinished in white, brown or simulated wood. This trim is far more stable than wood but cuts much the same, if not easier. What it lacks, however, is the warmth and varied grain pattern you can only find in real wood. While you’re at it, learn about car trim molding.