How to Glue and Join PVC Plastic Pipe
Updated: Nov. 02, 2020
The secrets to fast, leak-proof connections

Multiple Days
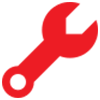
Intermediate
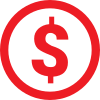
Varies
Introduction
How to make leak-proof connections fast, whether you're using PVC, ABS or CPVC. Plus, common mistakes to avoid and how to fix them.Tools Required
- Handsaw
- Level
- Nut driver
- Rags
- Tape measure
Materials Required
- Cement and primer
- Plastic pipe and fittings
- Transition coupling
Video: How to Glue PVC Pipes
Gary Wentz, an editor for Family Handyman, will show you how to glue PVC pipes to get a fast, leak-free seal.
Project step-by-step (7)
Step 1
Make Square Cuts for Strong PVC Joints
- Make an improvised guide by screwing together scraps of 2×4.
- Saw using a handsaw with a blade that’s 3 or 4 inches wide.
- Note: Square pipe ends fit snugly into the fittings, allowing plenty of contact area for the solvent cement to work. They also make a smoother interior surface for better water flow.
- Pro tip: Special saws for cutting plastic pipe are a worthwhile investment if you do much plumbing work. You’ll find them in the plumbing tool area or with the handsaws in most home centers and hardware stores. Otherwise, any fine tooth saw will work.
Step 2
De-Burr the Inside
- Roll a quarter sheet of 80-grit sandpaper into a tube and flatten it slightly to match the curve of the pipe.
- File off the inner burrs with the sandpaper.
- Hold the sandpaper at an angle and sand the inside and outside (see below) of the plastic pipe until you create slightly beveled edges.
- Note: Left in place, burrs can snag hair and other debris, causing clogs.
- Pro tip: You can remove burrs with a file or pocketknife, but sandpaper is easier to use and works great.
Step 3
De-Burr the Outside
- Knock off the outer burrs with sandpaper.
- Note: The pipe will slip into the fitting easier and you’ll get a tighter fit.
Step 4
Mark the Pipe and Fitting
- Dry-fit the pipe and PVC pipe connectors fitting, using a torpedo level if needed to align the fitting.
- Make a mark across the fitting and pipe.
- Pro tip: By the time you spread the solvent cement on both the pipe and the fitting and press them together, you have only several seconds to get the alignment right before the pieces are stuck together. That’s why it’s a good idea to make alignment marks beforehand on PVC joints where orientation is critical.
Step 5
Apply the PVC Cement
- Wipe the inside of the fitting and the outside of the pipe with PVC primer.
- Let it dry for about 10 seconds.
- Spread an even layer of solvent PVC cement on the inside of the fitting and outside of the pipe.
- Pro tip: To keep excess solvent cement from being pushed into water piping, don’t apply too much to the inside of the socket on the fitting.
- Note: Just swiping the pipe with cement and pushing on the fitting won’t ensure a strong joint. You want to make sure you have an even layer of cement over all mating surfaces.
Step 6
Push and Twist
- Align the fitting and pipe about a quarter turn from their final orientation.
- Push the pipe into the PVC pipe connectors fitting and twist the fitting until the marks are aligned.
- Pro tip: Twisting the fitting helps spread the solvent cement evenly to ensure a solid joint.
- Press and hold the pipe for about 15 seconds.
- Pro tip: If you let go immediately, the pipe may push out of the fitting, resulting in a weak joint.
CAUTION!
The solvent vapors from the PVC primer and cement can make you dizzy and are dangerous to your health. Make sure you have plenty of ventilation or wear an approved organic vapor respirator when working with PVC primer and solvent cement.
Fix Mistakes with a Coupling
-
- Note: Mistakes happen. Sometimes assembled PVC pipes don’t reach the predrilled hole because we dry-fit the PVC pipes and forgot to allow extra length for “shrinkage.”
- Saw out the bad section.
- Use a coupling to rejoin the parts, using new parts if necessary.
- Prime (if needed) and cement the parts together.
- Pro tip: Buy extra fittings. Having extras on hand will save a trip to the store. And you can return the extras when you’re done.
Step 7
Join Different Types of Pipe with Transition Coupling
-
- Note: Transition couplings have a flexible rubber sleeve surrounded by a metal sleeve and band clamps. They’re handy for connecting plastic pipe to cast iron, copper or steel, especially if you can’t thread on an adapter. Each coupling is labeled with all the different types and sizes of pipes it can join.
- Slide the pipe ends into the transition fitting.
- Turn the screws clockwise with a nut driver to tighten the bands and seal the joint.
Use the Proper Solvent for Each Type of Plastic
-
- Note:There are three common types of plastic plumbing pipe: PVC, CPVC and ABS. For a reliable seal, you have to use the solvent that’s formulated for the pipe. All of them contain aggressive solvents and adhesives, so beware of drips and spills.
- White or beige pipes (PVC and CPVC) also require a primer.
- You don’t need a PVC primer with black ABS pipe.
- Read the label to match the solvent cement to the type of pipe you’re using. Avoid universal solvent cements.
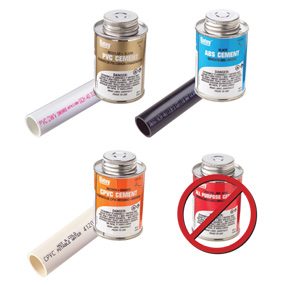