Learning these basics will help you embrace the allure of woodturning — uncovering astonishing beauty in a chunk of wood.
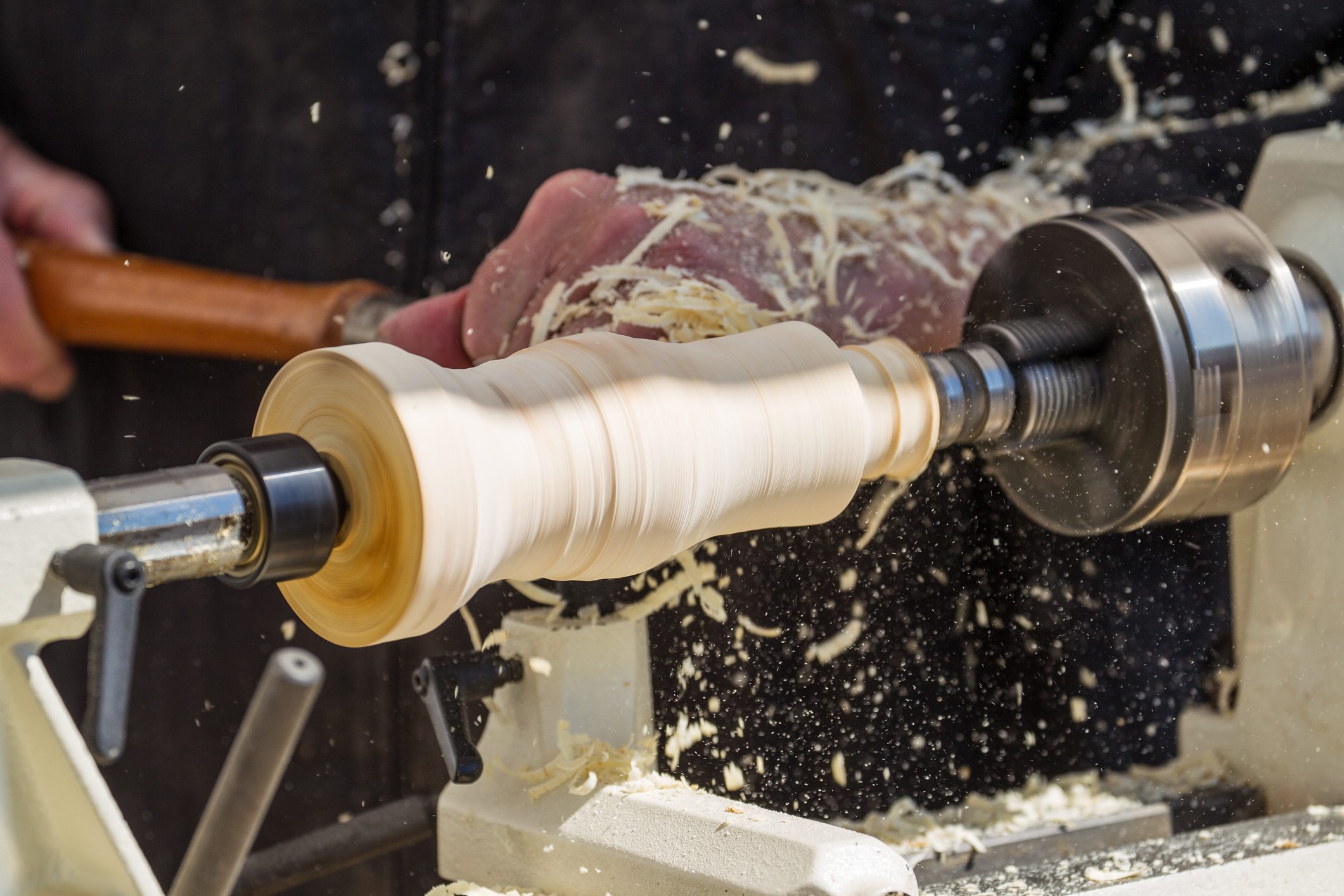
The Basics of Woodturning
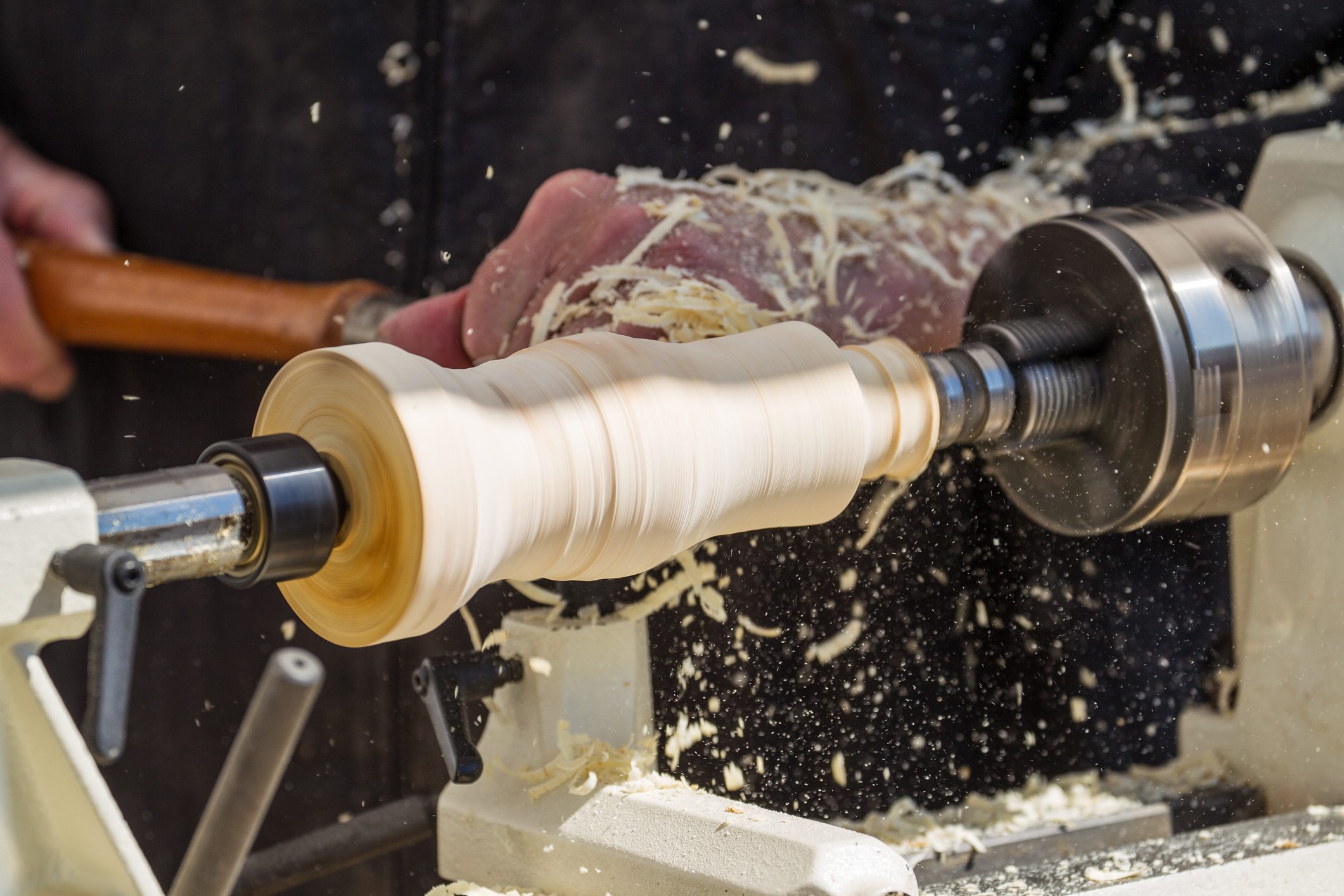
I started working on woodturning projects five years ago because I wanted to make rolling pins for lefse, a traditional soft Norwegian flatbread.
In researching my second book on lefse, Keep On Rolling!, I learned of a guy in the early 1900s who made more than 150 lefse rolling pins for Norwegian-American bakers in his region. I wanted to be like him — not just making reliable standard pins but functional pieces of art, using handsome hardwoods as well as woodturning tools and techniques.
That’s what I’m doing today, along with four other members of the Minnesota Woodturners Association. I sell these pins online and at markets, and give some away to friends.
There are two overriding reasons why I turn wood:
- I enjoy discovering the astonishing beauty in a chunk of wood and the artistic talent I never knew I had.
- I love the reaction when I give someone something I made. Let the wood do the talking and watch the faces light up!
What Is Woodturning?
Woodturning is a form of woodworking involving a lathe. With other kinds of woodworking, the wood is stationary and the tool moves to create cuts. In woodturning, the lathe turns the wood on its axis at high revolutions per minute while relatively stationary special cutting tools on a tool rest do the work.
A wood lathe allows woodturners to create all kinds of objects, from bowls to stair railings to chess pieces to musical instruments.
History of Woodturning
The art on monuments in ancient Egypt offers the first recorded instances of spindle turning. These illustrations showed a strap a helper used to rotate the lathe while another worker cut the wood.
The ancient Romans, Chinese, Persians and Arabs had their own variations of the lathe. Early lathe workers would sometimes hold cutting tools with their bare feet while powering the lathe with their hands.
In the 19th and early 20th centuries, woodturners in England employed the master-apprentice system in turning shops, where they crafted cups and bowls as well as detailed tables, chairs and staircases. In Germany and Russia, woodturning was concentrated in villages that specialized in turning toys.
In the U.S., woodturning was part of the industrial arts curriculum in public schools, often a prerequisite for furniture-building classes. In the 1970s, interest in hobby woodturning in the English-speaking world flourished, reviving all things woodturning.
Basic Woodturning Terminology
When you read about woodturning or talk with woodturners, these are some terms you’re likely to encounter.
Bevel
The area beneath the cutting edge of a scraper or gouge. The bevel on a gouge is always held in contact with the wood.
Blank
A piece of wood rounded smooth or cut into a section for lathe use.
Burl
An unusual growth on a tree, producing swirls and other interesting grain patterns.
Chuck
A device that holds the workpiece on the lathe.
Headstock
Provides the drive for the workpiece, usually through pulleys connected by a belt to the drive motor of a lathe.
Heartwood
The fully developed wood surrounding the core, usually darker than sapwood (see below) and really dense.
Moisture content
Percentage of water weight to total weight. Moisture content is usually 30 to 40 percent or more when wood is freshly cut (aka “green”). Dry wood typically has moisture content of less than seven to eight percent.
Sapwood
This surrounds heartwood and is usually softer. It transports sap from roots to leaves. It’s a different color than the heartwood.
Spalted wood
Wood in the process of fungal decay that shows as black lines in the grain. Woodturners prize spalted wood because the black lines add an artistic element to the turning.
Tailstock
The movable assembly opposite the headstock that slides along the lathe bed and supports workpieces.
Basic Woodturning Methods
These are the ways woodturners execute their craft.
ABC turning
Anchor/bevel/cut, or ABC turning, is the only safe method to start a cut. Anchor the tool to the tool rest, bring the bevel in contact with the spinning wood, then slightly adjust the angle of the tool until the cutting edge begins to cut.
Spindle turning
Requires mounting wood between the headstock and tailstock, then turning the spindle to create intricate designs.
Segmented turning
Pieces of wood glued together form a blank for turning. The combination of different wood grains and textures creates unique patterns.
Faceplate turning
The woodturner attaches a circular metal plate to the end of the lathe. This stabilizes and holds wood for smoother turning, especially with large blanks of wood.
Bowl turning
A gouge bevel forms a blank into its final shape. This technique uses scraping tools to smooth out the hollow surface and create a seamless bowl.